ELMO Design

ELMO is designed with the purpose of being a test bed UAV to evaluate the performance of a range of electric engine configurations. As such, ELMO is a conventional and stable flight platform with the modularity capability integrated throughout the airframe that allows ELMO to fulfil its research aim.
Wing
-
Designed to produce a certain amount of lift at cruise speed and take-off.
-
Combination of ribs and spars to guarantee stability.
-
Flaps to achieve high lift performance.
-
Ailerons added for roll control.
-
Servos for control surfaces.

Tail


-
Evaluated to have the best shape and components.
-
Vertical plane under fuselage in order to provide additional rudder area and protect the propeller.​
-
Lower stabiliser outside of wake of horizontal plane, perfect for spin scenario.​
-
Control surfaces managed by inline servos.
-
The rudder is optimised to counter any possible propeller failures.
-
3D printed parts to hold structure together.
Fuselage
-
Carbon fibre landing gear designed to withstand excessive loading.
-
Steerable nose gear.
-
Carbon fibre sandwich bulkheads to transfer loads to main spar.
-
Nose designed in tandem with landing gear and easy to remove.
-
Central structure held together by spars and attachments
-
Brackets in order to secure flight if there is a bonding failure.
-
Physically tested up to 170N.
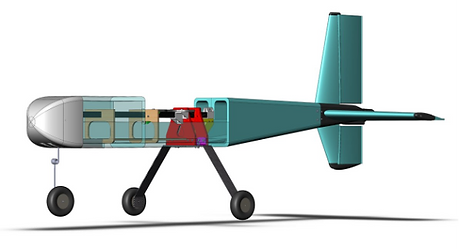

Avionics
Flight Controller
-
Includes autopilot mode.
-
Easy to set up and open source software.
Receiver
-
Small and light.
-
Up to 16 channels.
Power Units
​​​
-
710W motor in fuselage and 340W in wings.
-
Tractor or pusher tests on the wing.
-
Upper and lower surface of wing tests.
-
Designed to be positioned in any wing propulsion layout.

ELMO's Research Configurations


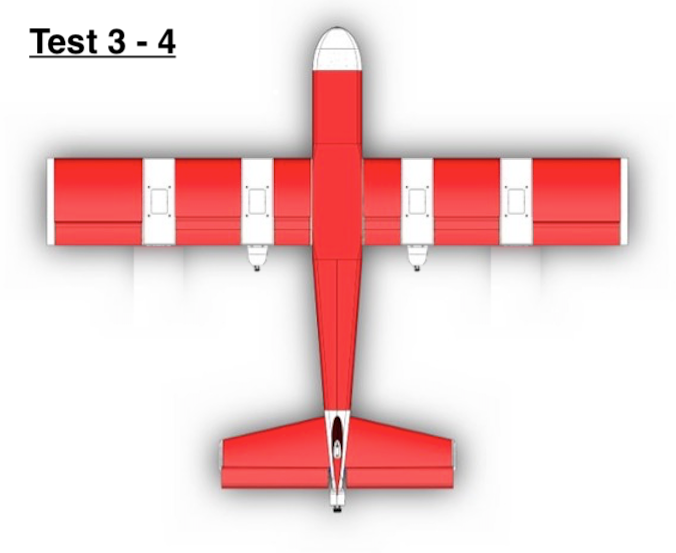
